Pelleting Experience of Wood Sawdust
Processing the wood sawdust to pellet requires not only quality equipment but also experience, experienced operators can judge the condition of sawdust and adjust the status to improve the pellet mill production efficiency and enhance the pellet quality.
SIMEC supply high quality pellet mills for global wood pellet factories, most of our customers are experienced at biomass pellet making, the followings are some of the experience they summarized in the production process, manufacturers can take these as references.
While the material is powder less than 5mm, the moisture is about 13%. Please specially arrange one worker to check the moisture of sawdust when the sawdust is sent to factory. You should place the sawdust based on the moisture separately, If the moisture is much lower, please spray some water to more than 10% moisture and let the sawdust to have some time (more than 2 hours) to resorb the water inside before production, and you can add extra 2-3% water during the production; If the moisture is too high, please dry them or add some dry sawdust and mix them together, guarantee 12-14% moisture equally; when the wood sawdust is too fine powder, please mix some 3mm size of wood sawdust together to strong the wood pellets; please mix hard and soft wood sawdust together for improving the production capacity.
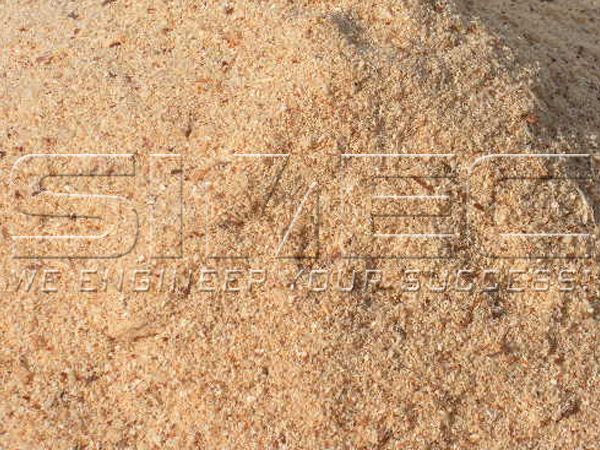
1. The moisture of sawdust is very important for the smooth pelleting. In order to strictly control the moisture, we can adding a little water and 0.5-1% oil by mixer which can make sure the moisture of sawdust material is 12%-14%. Also, it is very necessary for pelleting smoothly. When the moisture of wood sawdust is more than 15% and too wet, the pellets are cracked with some powder, it is not good pellets ,and even the pellet mill can not make the pellets. When the moisture of wood sawdust is less than 11% and too dry, it is very difficult for the pellet mill to make the wood pellets and even can not make the pellets; at same time, it will heavily damage the pellet mill. Please do not do that forever! When you find that the pellet mill works very difficultly, you must check the moisture of wood sawdust at once. Please note that only 12-14% moisture of sawdust can guarantee the pellet mill works smoothly and get beautiful pellets, and avoiding any damages to pellet mill!
SIMEC Pellet Mill SPM420 have water adding system, at conditioner there is a water pipe, it can add water into the raw material to adjust the moisture to the proper content for better pelletizing. The pipe is connected on a dial gauge that shows the volume of water, making it easy to be detected and controlled.
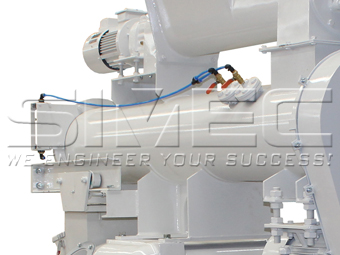
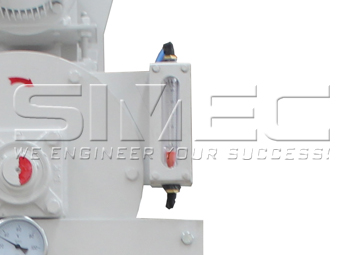
2. Please pay attention that the pelleting will be very difficult if the sawdust is very dry, also it can cause a large amount of dust in the pellet chamber. At that time, if there is iron scrap in the pellet chamber, it is easily to cause spark which can burning the dust. That is very dangerous.
3. (1) While there are grass powder material in the formula, it is necessary to use forcible feeder to feed evenly in to the pellet chamber. Also, paddle feeding should be used to keep feeding evenly. Or (2) While there are grass powder material in the formula, we can also use screw vane forcible feeder, there is one half screw vane in the discharging outlet of the forcible feeder which can make sure feeding evenly and would not block the pellet pressing chamber. If the materials are with the thick wood chip, the thick wood chip maybe block the feeder and also damage the forcible feeder motor. Please note it carefully.
4. Adjust the clearance between the die and roller to 0.15mm-0.3mm.
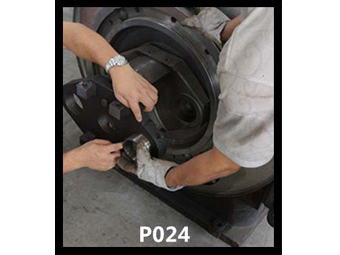
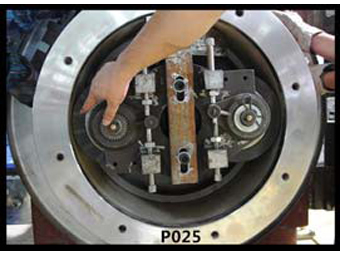
5. Before using new die, firstly mix the 30% carborundum (fine sands), 70% crushed bean bran or rice bran and a little of grease, secondly polishing the holes of the die by the mixture about twenty or thirty minutes. While the die being heat and the inside hole of the die is very smooth, it can start to pellet sawdust.
6. Adding the high temperature lithium grease (more than 200 degree) into the rollers and main bearing from the three oil hole at the end of main shaft every two hours while producing (Do not turn off the pellet mill). Adding the high temperature lithium grease (more than 200 degree) to the roller about 10 times by grease gun. It should be make sure the lithium grease have been added into the roller for lubricating, or else the bearing of the roller is easily to be burned out.
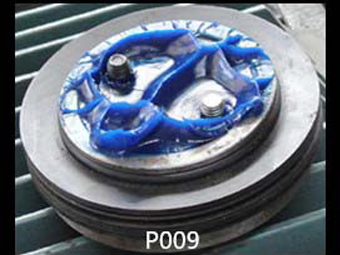
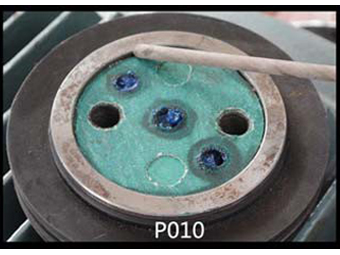
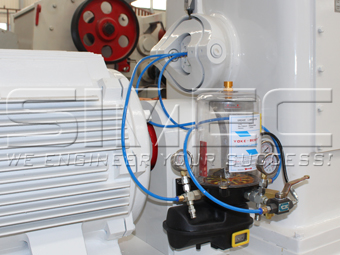
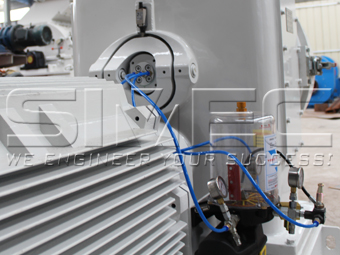
7. While running for some time, the clearance between the roller shaft and copper sleeve will be larger and lager. Then while adding oil the oil will seep from the big clearance but not enter into the roller which can result in burning bearing. So please replace the copper sleeve and “O” ring in time.
8. While producing, please use fan to resorb the steam from the steam outlet or outlet of pelleting chamber of pellet mill continually. The large amount of steam will change the moisture of sawdust inside the pellet chamber and mixing conditioner and then the pelleting is difficult also. If you find a large amount of steam that means the pellet temperature is rising which will result in difficult in pelleting or blocking. At that time, please immediately turn off the screw feeder as then the sawdust is pelleting slowly, also, the temperature of the die is more and more high. The operator can feed the sawdust pellet with 3-5% oil into the pelleting chamber manually through the impaction door on the chute; the hard sawdust pellet will drill through the blocked hole under the high pressure. After that, slowly start the feed screw to begin producing.
9. While normal producing, please guarantee that the feeder can continue feeding oiled sawdust into the die without any stops. if operator stop the pellet mill for some times for rest, or the oiled sawdust can not fed into the die more than five(5) minutes, please manual feeding some sawdust with high oil(3-5%) into the hole of dies. When operator re-start production, firstly manual feeding some mixtures of sawdust and 3-5% oil into die, die will be hot and can produce the pellets smoothly ,and then start the feeder slowly and then go on producing normally.
10. If the temperature of die is higher than 75℃, the fiber will quickly expand which result in the block and discharging difficult for die. The operator should immediately shut off the machine to reduce the temperature of die while find the length of the sawdust pellet is about 5mm and strange knocking on the door cover accompany with a large a mount of steam overflowing. At that time the rollers are flopping to damage the die and main shaft. Then firstly clear and brush the inner of die with oil, then start the pellet mill meanwhile manually feed the sawdust pellets which mixed with the oil(3-5%), if it can unblock the die hole, then normal production. If not, please discharging and cleaning all the blocked holes of die, and then the pellet mill can be go on working. Please pay attention on that it is dangerous to producing while the die hole is being blocked which would destroy the pellet mill.
11. Everyday after finished the production, please manual feeding some sawdust with high oil(3-5%) into the hole of dies. And the turn off the machine and clean the pellet chamber. Brush the inside of the die by oil and let the oil permeate to the die hole. While the machine is cool, the sawdust will shrink and oil will lubricate the hole of dies. Then next day, please start pellet mill for 10 minutes, firstly manual feeding some mixtures of sawdust and 3-5% oil, die will be hot and can produce the pellets smoothly ,and then start the feeder slowly and then go on producing normally. For the operator, the experience of prevent blocking is very important. Most of blocking problem is caused by the mistakes of operation. To pellet different materials need different operation experiences, please collecting the experience at site.
Except for the main points mentioned above, customers should sum up experience in actual production process, moreover, proper and quality equipment makes the production process easier and cost saving, SIMEC Pellet Mill is customers’ wise choice.