Forced Cycle Lubricator for SPM780 Pellet Mill
Lubrication is very important for wood pellet mill. SIMEC SPM series pellet mill adopts advanced forced cycle lubricator to guarantee the continuous operation of pellet machine. These lubrication system is centralized automatic, liberate the labors.
Forced Cycle Lubrication System of SPM780
1. Operation
YLS-Z Forced Cycle Lubricator is used for continuous lubrication. Via the control from additional timer, it can operate at interval lubrication also. The recommended oil viscosity is 30 ~ 250 cSt at unused condition.
The maximum output volume is 7L/min and the volume is adjustable. The output can be discharged in three output bores. The filter is set at both inlet (suction end) and outlet. The Output Pressure is adjustable and set at 5kgf/cm2. Pipe block sensor is installed at the outlet filter. When the pipe is stocked, the sensor will release the signal to the exterior controller to stop the machinery. Flow sensor is installed at output bore to inspect if the output flow is at normal condition.
2. Flow diagram
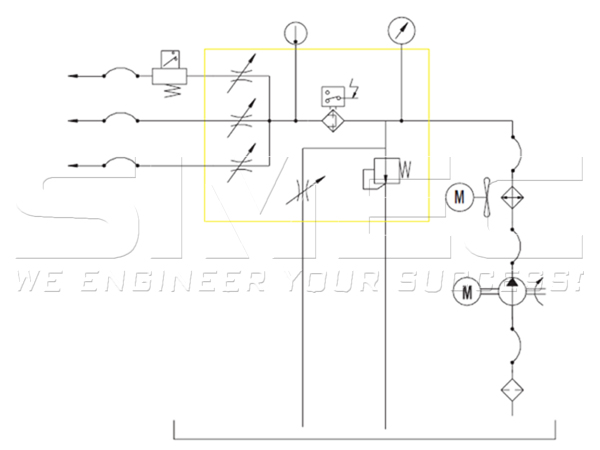
Flow Diagram
3. Parts of the lubricator
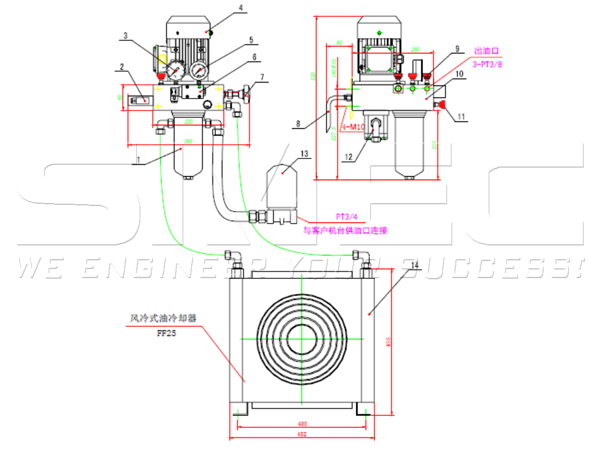
Parts of the Lubricator
- Filter WU-E40×100BDP 1 pcs
- Flow Sensor 1 pcs
- Thermometer XY-004 WSS 1 pcs
- Pump Module 1 pcs
- Pressure Gauge 0—2.5Mpa 1 pcs
- Pipe Block Detect Sensor 1 pcs
- Pressure Adjustment Handle 1 pcs
- Cycling Pipe 1 pcs
- Governor Valve 3 pcs
- Module Block 1 pcs
- Throttle Valve 1 pcs
- Gear Pump 1 pcs
- Filter at suction end 1 pcs
- Fan Type Radiator FF25 1 pcs
4. Specification
2. Working Pressure:P=0—0.5Mpa
3. Motor:N=0.37Kw,415V ,50Hz n=1450rpm
4. Fan Type Radiator:220VAC,50Hz,75W , Pressure-proof at 2MPa
5. Flow Sensor:220V 3A
6. Filter at output end:WU-E40×100BDP
7. Pipe Block Detect Sensor:220V 0.35Mpa
8. Filter at suction end: 100μ/25L
5. Installation
1. Pipe connection must be reliable without leakage. The pipe cannot be over-bended to avoid damage.
2. The recommended oil viscosity is 30 ~ 250 cSt at unused condition. The refilling is at the full level. The air filter must be tightly twisted to avoid particle. At normal operation, the lubrication needs to be replaced yearly. Daily inspection at the lubrication level is necessary. If the lubricant is below the normal level, refilling is a must.
3. The Motor is at 415V/50Hz/0.37Kw. The Fan Type Radiator is at 20V/50Hz/75W. The pipe Block Detect Sensor is 220V/0.35MPa. The pressure gap between the two ends of the filter over 0.35Mpa, the sensor will release signal. The Flow Sensor is 220VAC/3A to release signal when no flow. The circuit design should be time-delay circuit because there is no flow when the motor starts for a short while.
4. Output Pressure and Output Volume are fixed. Only if necessary, they are adjusted by (7)Pressure Adjustment Handle, (9)Governor Valve, and (11) Throttle Valve.
5. When power is “ON”, the motor and fan type radiator stars, the lubricant is sucked via (13)Filter to the gear pump to discharge to the fan type radiator, then enters (10) Module Block. The excessive lubricant will return the tank in either Pressure Adjustment Handle or Throttle Valve. The cooled lubricant flows through (1)Filter and discharged in into three output bores to export to lubrication points. One of the three output bores is installed with (2)Flow Sensor.
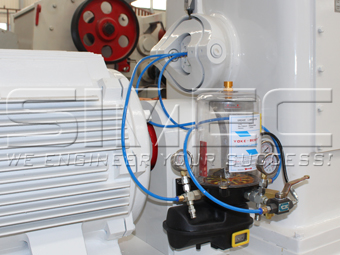
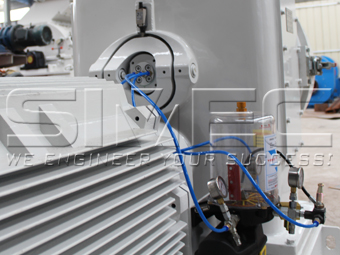
6. Notice
1. The recommended oil viscosity is 30 ~ 250 cSt at unused condition. The refilling is at the full level. The air filter must be tightly twisted to avoid particle. At normal operation, the lubrication needs to be replaced yearly. Daily inspection at the lubrication level is necessary. If the lubricant is below the normal level, refilling is a must.
2. The core of the filter at output end is necessary to be cleaned monthly by gasoline or kerosene. The filter core should be replaced every year. When the Pipe Block Detect Sensor releases abnormal signal, the filter core needs cleaning.
3. The surface of pressure gauge and the thermometer need to be protected without damage.
4. Output Pressure and Output Volume are fixed without adjustment.
5. Pipe connection must be reliable without leakage. The pipe cannot be over-bended to avoid damage.
6. Fan type radiator needs cleaning timely by compressed air to remove the particle.
7. Consumption Part: The filter core WU-E40×100
7. Faults
Malfunction |
Symptom |
Cause |
Rectification |
Note |
|
Alarm at Starting |
Without |
To install time-delay circuit |
No flow when the motor starts for a short while |
|
|
Check if lubricant in the tank is enough |
Refill the tank |
|
Check if the filter at the suction end blocks |
Clean the filter |
|||
Check if the filter at the output end blocks |
Clean the filter |
|||
Check if the gear pump is broken. |
Change a new gear pump |
|||
Alarm of the Pipe Block Detect |
Signal released |
Dirty Lubricant |
Clean or replace the filter core. |
When the filter at the output blocks, the motor may get hot and noisy. |
Choosing a good equipment can save cost of labor as well as improve the efficient of production. SIMEC is wise choice for pellet manufacturers. With more than 20 years experience, we provide not only high quality equipment, but also thoughtful and professional after sales services such as installation, commisioning, training and so on.